On March 18, BYD announced its Super e-Platform boasting an impressive 1 megawatt charging capacity, making charging speed on par with gas refueling.
The same day, CATL and NIO announced a partnership on battery swapping, aiming to, again, making EVs as fast to refuel as ICE cars by simply swapping the empty battery with a full one.
Just a day later, on March 19, Porsche Engineering revealed its intriguing 'AC battery' concept, which can use AC current directly to recharge, without needing an inverter.
These three press releases all imply some pretty cool innovations around EV battery architecture, albeit in pretty different ways, so I figured it’d make for a pretty interesting deep dive.
Today’s part 3 will focus on Porsche and AC batteries.
AC batteries: the concept
The concept is outlined in details in this graph the press release from Porsche :
That makes total sense, right? I guess not, unless you’re pretty deep into battery electronics, so let me break it down.
Some background on AC and DC
Let’s start with the basics : what happens when you press the pedal of an EV?
In most modern EVs, you’d be driving a voltage and current signal to a Permanent Magnet Synchronous Motor (PMSM) that drives the wheel. Basically, a device that converts electric energy to rotation through interaction with permanent magnets.
However, you may recall that a battery sends DC signals (constant current). Our PMSM however, in order to drive the magnetic field, needs an AC signal, one that varies in time like a sinewave. That’s usually done through silicon carbide (SiC) semiconductors that perform Pulse Width Modulation (PWM), see graph below:
Basically, by making the battery pack quickly alternate between DC pulses of varying width, these semiconductors will generate a sinewave (AC) that can be used by the motor to drive the wheels.
Some background on series or parallel arrangements
If you recall from part 1 of this series I showed that we could wire the modules in the Porsche Taycan differently; for the same total number (396) you could have 99 in series and 4 in parallel, or 198 in series and 2 in parallel :
The only thing that would change was the pack voltage : 400V or 800V, depending on the configuration.
Porsche main innovation : dynamic configuration
Now, usually, this wiring (99s4p or 198s2p) is something that engineers have to decide in the design phase and then remains fixed throughout the lifetime of the vehicle.
The main innovation of the AC battery concept by Porsche is to be able to change the module configuration on the fly. What the engineers have done is develop electronic circuits (I’ll come back on this) that can dynamically switch around these modules, like in this figure:
My understanding of what is going on in this graph is the following:
First, 6 modules are in parallel (1s6p). The whole is at the same voltage as a single module since voltages are equal in parallel so the voltage is low. Then, they switch to 2s3p, so the voltage increases. Next, they switch to 3s2p, the voltage increases again. And it goes on until all modules are in series and the voltage reaches its maximum value.
With more modules (like 396 in the Porsche Taycan), it is possible to have a smooth voltage function, pretty similar to the one coming out of Pulse Width Modulation.
Now, being able to change electrical connections on the fly is not trivial (they obviously can’t send someone manually rewiring your Porsche Taycan every second).
On the figure we can essentially see 8 MOSFETS (Metal-Oxide Semiconductor Field Effect transistors) per module that switch on and off to activate different modes : in parallel, in series, or bypassed.
And finally, to get an AC voltage usable by the motor you need three phases (three shifted sinusoids), so you actually need to separate the modules into three independent units, like here on the figure:
And that’s how you can get an AC voltage, without requiring silicon carbide (SiC) semiconductors that perform Pulse Width Modulation.
But … what for?
Aside from cool engineering proof-of-concepts, what does Porsche get out of this?
Space efficiency
This electronics allows to get rid of the inverter, which can take up a significant amount of space in the vehicle (probably over 10L, although that will vary a lot from vehicle to vehicle) which frees up space for the battery pack or other components.
The cooling system can also probably be distributed more efficiently, since in the absence of inverter most of the heat generation is coming from the battery modules.
Pulse charging
A cool concept that hasn’t quite taken off so far is pulse charging. The general idea is that instead of feeding the battery a constant current (CC) (see profile a) on the next figure), you instead quickly alternate between current pulses and rest phases (see profile d) on the next figure). Some studies claim advantages of pulse charging on battery lifespan.
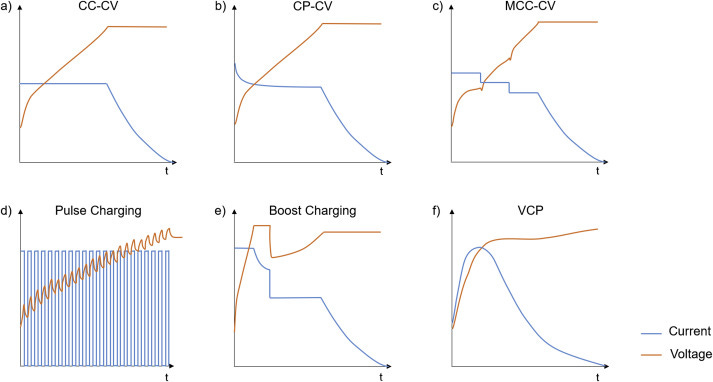
The main problem of pulse charging is that, if you want to keep the total charging time constant with respect to CC-CV, you basically need to double the pulse current (since you have equal rest periods between the pulses). That’s pretty demanding of the chargers, which limits are already being pushed in terms of current (see part 1 of this series).
But with Porsche’s AC battery concept, during the "pulse" phase, you could configure half the modules to receive the full charging current while the other half are bypassed or in rest mode. Then you flip it : the previously resting modules get the charging current while the others rest. The charger itself just sees a steady load, but each module experiences the pulse/rest cycle that's supposed to be beneficial for lithium-ion chemistry.
Safety and serviceability
Being able to bypass different modules can be interesting from a maintenance standpoint : a module that degrades faster than the rest will limit the performance of the whole pack, but if you’re able to bypass it you can spread the load among the ‘good’ modules. And when you head to the garage for maintenance, the operators can bypass the module and replace it without having to shut down the entire pack or deal with high voltages across the full string.
I assume there might be other advantages in vehicle-to-grid applications, although I am not sure how easy that is to implement in practice.
Where is this concept headed?
Porsche is not the only company to explore the concept of bypassing and switching modules or even cells.
Stellantis and Saft have been exploring the concept for EVs as well, and in the stationary sector startups such as SwitchESS in France and Relectrify in Australia are going one level down : switching on and off cells to generate the AC sinewave and get rid of the inverter.
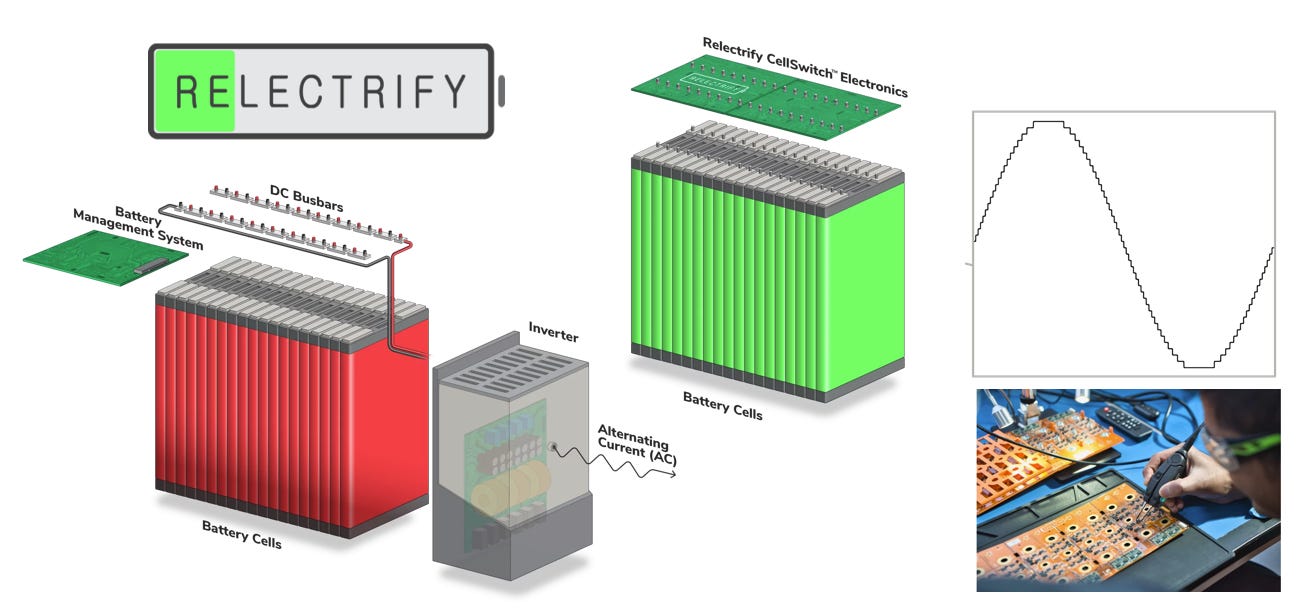
It’s an interesting concept, but it remains to be seen how robust it is in practice. Because yes, inverters are fairly expensive and take up space, but they’re also a really mature and reliable technology (and engineers sometimes have this tendency to find complex solutions to simple problems).
Nevertheless, I am really curious to see where this concept goes in the near future !
🌞 Thanks for reading!
📧 For tips, feedback, or inquiries - reach out
📣 For newsletter sponsorships - click here