To compromise or not to compromise in battery technology
Damien Frost, CTO and Co-Founder of Brill Power, gets us up to speed with the challenges presented by large format cells, and how finding the way forward between compromise and innovation will lay the path for the future of the industry.
Chemistry choices
The evolution of battery chemistries plays a pivotal role in various industries, influencing everything from consumer electronics to electric vehicles and renewable energy storage. Among the most prominent battery chemistries are Nickel Manganese Cobalt (NMC) and Lithium Iron Phosphate (LFP).
Understanding their development, advantages, challenges and future trends is critical for appreciating their impact on modern technologies. But it’s crucial to remember that in battery technology, compromise has been the modus operandi over the years to be able to meet demand. Balancing performance, cost, safety and environmental impact is complex. An ongoing challenge within the industry is how to best balance cost with energy density, and then ensure that the maximum energy from each battery pack can be extracted.
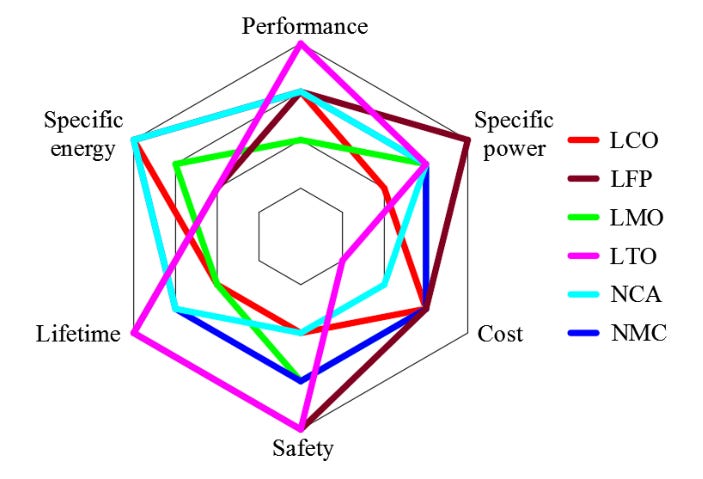
As the car industry started its transition to battery-electric power from ICE engines, NMC cells dominated the market thanks to their maturity in the market and energy density which started to make sense for automotive applications. However, their advantages come with challenges related to cost and material availability. The extraction of materials like cobalt poses ethical and environmental questions. As well as this, NMC cells are among the least safe of lithium-ion chemistries and are prone to instability under certain conditions.
Because of these drawbacks, the stationary storage market and even some products in the automotive industry have shifted towards using LFP cells. In the light-duty vehicle sector, the market share of LFP cells grew from only 3% in 2019 to 27% in 2023, driven by the dominance of the Chinese market. In applications where energy density is not critical like stationary storage, LFP has become by far the dominant chemistry, driven mainly by significant reductions in cell prices but also by the reduced risk of overheating and fire. Users have ‘accepted’ the compromise of accessing a lower energy density with LFP cells – but are keen to find a way to overcome this inherent limitation of this chemistry.
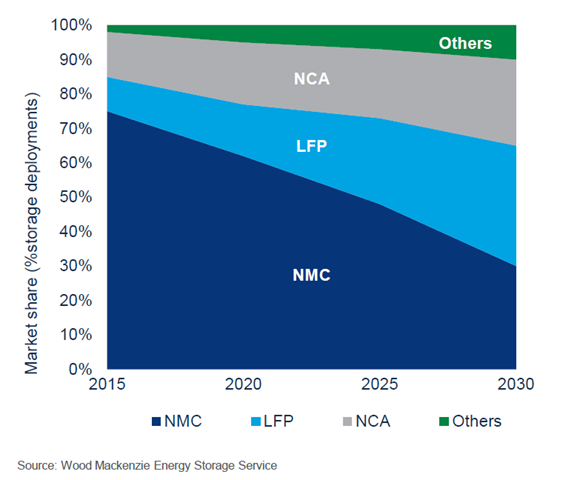
Progressing to larger cells
As part of the drive to continuously reduce cost and improve efficiency, the industry is also moving towards larger cell capacities. These cells, which now exceed 500 Ah (ampere hours) compared to the more conventional 280 Ah cells currently used, offer several advantages including higher capacity and energy density. Since larger cells can store more energy, it makes them ideal for applications requiring high power output, such as electric vehicles and grid storage. Using larger cells can reduce the number of cells needed for a battery pack, simplifying the design and lowering production costs.
But the trend of moving towards LFP chemistry alongside larger cell formats presents challenges for battery management and health monitoring. Larger cells generate more heat which can cause an uneven temperature distribution within the cell. Managing internal temperature variations is crucial to prevent hotspots that can degrade battery performance and safety.
Monitoring the State of Charge (SoC) and State of Health (SoH) of individual cells within a full pack becomes more complex with larger cells. The use of traditional methods may not be sufficient, and advanced algorithms and robust monitoring systems may be necessary to ensure the reliability and safety of the system.
Adapting BMS technology to meet these demands is critical to support the continued development of battery technology.
Focusing on the health of individual cells
The shift towards larger cells also necessitates a closer look at the health of individual cells. A small failure within one of these large cells can significantly reduce its capacity or take it down entirely, more so than a single failed cell in a pack of smaller cells.
In the early days of Tesla, for example, each of the small cells in parallel was connected to the bus bar. If one cell failed or short-circuited, the fuse would blow, isolating the failed cell. This design reduced the impact of a single failed cell, increasing the overall robustness of the pack.
But with today’s larger cells, a single cell failure can lead to an entire string being taken offline. Further, in most large battery designs, there is no easy way to isolate a failed cell. To address these challenges, it is essential to develop BMS with built-in redundancy, leveraging clever technologies such as real-time monitoring, predictive analytics and fault-tolerance mechanisms.
These innovative solutions enable the BMS to accurately assess cell health and isolate faults within individual cells, even in large-cell configurations, to prevent failures from affecting the entire battery pack. By integrating such technologies into BMS design, we can ensure that battery packs remain reliable and safe, even as cell size increases.
Focusing on large format LFP
The challenge of large format cells is compounded by the fact that measuring and reporting accurate SoC and SoH is far more challenging with LFP cells. Developing and delivering SoX algorithms involves many steps, with minor errors at each stage having an exponential impact on the accuracy of SoX for LFP systems thanks to its flat OCV curve.
Developing accurate SoC & SoH algorithms involves four key steps. Testing LFP cells requires several steps and at Brill Power, we optimise battery cell measurement using this four-step and in-house closed loop process:
LFP cell testing using high-accuracy lab equipment resulting in a cell model
Combining this cell model with BMS measurements from low-cost current, voltage and temperature sensors to deliver SoC estimation
Tuning and validating the cell model and estimation algorithm based on software-in-the-loop and hardware-in-the-loop testing
Once in operation, uploading detailed (cell-level) measurements and estimations to the cloud, and assessing the accuracy. Fine-tuning algorithms and remodelling based on real-life accuracies compared to the original tests
Within the battery industry, this is often a disjointed process, with a number of companies involved. Doing this within one company reduces the likelihood of errors being compounded to deliver a more accurate SoC of the system.
As for the use of bigger cells, the challenges increase with size and with more difficulty to accurately monitor cell temperature on the surface and inside the battery.
Improving SoC estimation is crucial for increasing the amount of usable energy system owners and operators can extract from their battery systems, ultimately minimising one of the major compromises of LFP technology, especially in electric vehicles where SoC drives range estimates.
‘The future of compromise’
Industry’s and end users’ acceptance of LFP from NMC reflects a strategic and direct response to the pressing demands for enhanced safety, reduced costs and more reliable and environmentally friendly sourcing. Although this transition involves trade-offs in energy density and challenges in SoX estimation, the drive to minimise these compromises is pushing the boundaries of innovation.
Emerging chemistries like sodium-ion batteries offer exciting possibilities, yet challenges remain. In the short term, increasing cell capacities, novel BMS solutions and innovations to optimise SoX throughout the lifetime of a system will be fundamental in the pursuit of batteries that offer fewer compromises and shape the next generation of energy storage solutions.
Ultimately, the future of battery technology lies in the industry’s ability to innovate beyond current limitations, creating systems that balance performance, safety and sustainability without significant compromises.
🌞 Thanks for reading!
📧 For tips, feedback, or inquiries - reach out
📣 For newsletter sponsorships - click here