Three Months as a Graphite Girl
Our editor Issy spent 3 months working at Vianode, a synthetic graphite manufacturer in Kristiansand, Norway. Here’s her reflections and ponderings for the emerging European Graphite industry.
I stumbled across Vianode at the ECS conference in Gothenburg in October 2023. In the third year of a Faraday Institution PhD studentship, we are encouraged to take 3 months out to spend some time in industry or a different research environment. It’s a privilege to be supported to take these opportunities, and I was determined to find something where I could go somewhere new and learn something different. Vianode kindly agreed to have me, and I was excited to learn about sustainable battery materials manufacturing.
I had never been to Norway before. I booked my travel, three months in an Airbnb, and decided to take my bike with me to help carry my things and to save me having to buy or rent one (it looked very expensive). I left Birmingham about midday on a Friday, and wound my way on an overnight train to Berlin, from where I wiggled to the top of Denmark and finally caught a ferry on a Sunday morning to the city of Kristiansand, in Norway.
My first impressions of the city were that it was very industrially beautiful on that clear cold day, as I pushed my three months worth of possessions up one of Kristiansand’s many unbelievably steep hills.
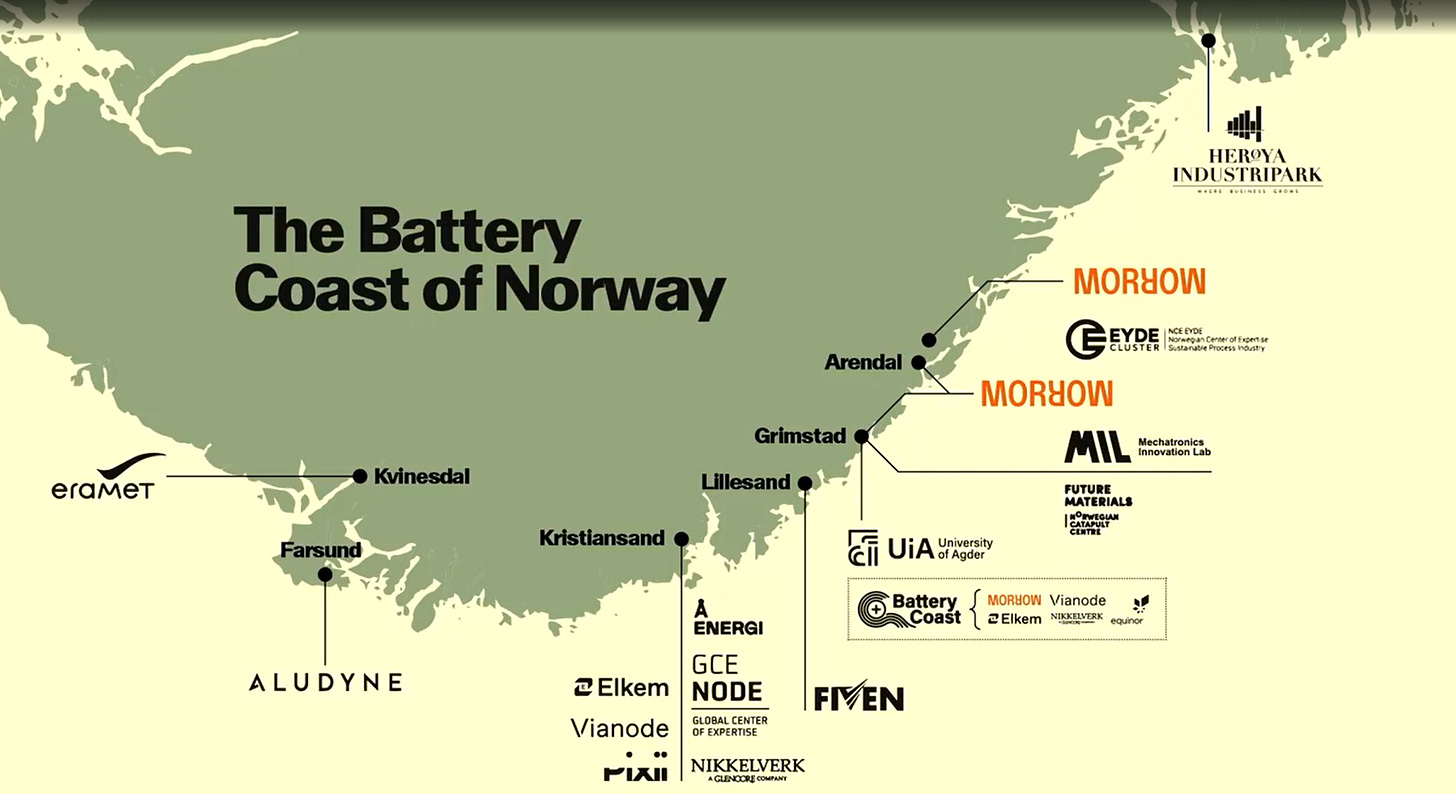
Vianode is based in the city of Kristiansand on the southern tip of Norway. It’s part of an academia and industry cluster called the ‘battery coast’ which includes the University of Agder, Morrow, and various other parts of the battery supply chain including Elkem, Nikkelverk and Å Energi.
The company itself was spun out of Elkem, which has over 100 years experience in manufacturing carbon materials and more recently silicon, and is now owned by industrial and financial companies Hydro and Altor.
I was based in Vianode Technology Centre. It has a pristine lab with grey floors and around 25 friendly scientists and engineers. The lab and office space was a 10 minute walk down to the industrial pilot plant, which can produce over 200 metric tonnes of graphite a year. The whole site is on the coast, and on a blue day you could walk down to the pilot watching the sparkle off the sea.
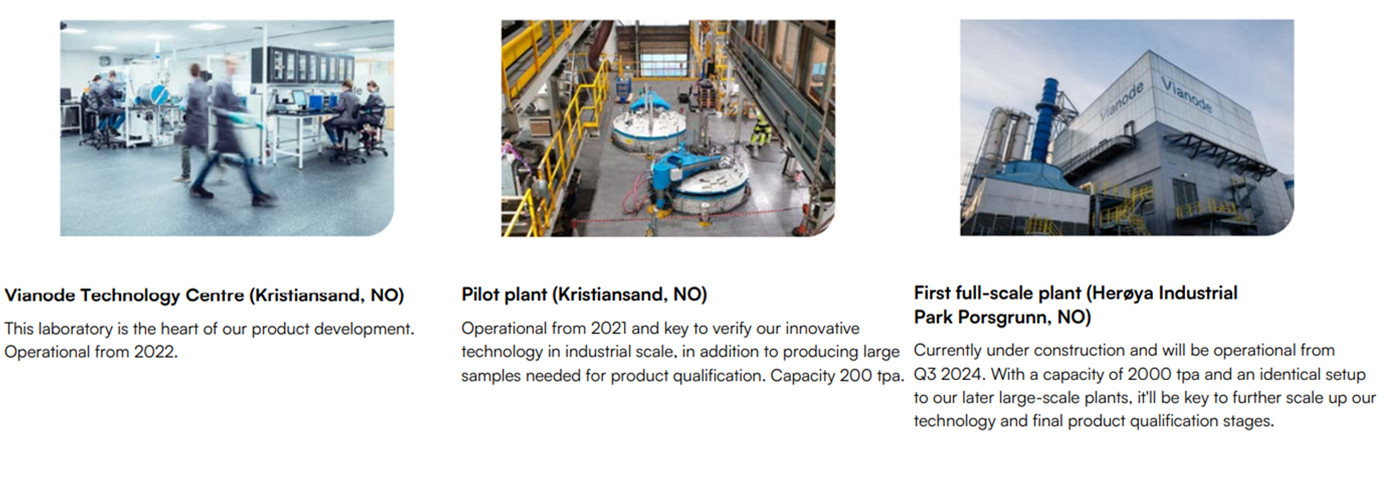
The first full scale plant is currently being built at Herøya Industrial Park, which will produce up to 2000 tonnes of graphite a year once operational, and there are plans for a larger plant in North America, to produce 60,000 tonnes per year. The long-term ambition is to supply advanced battery materials to 3 million EVs per year by 2030.
Synthetic vs Natural Graphite
Synthetic graphite is made from petroleum coke, which is a waste product of oil refineries. The black coke powder is characterised, since every refinery and even each different oil feed will result in a slightly different coke product. Those that meet the criteria are calcined, shaped, and graphitised at >2500°C. Long term, the phase out of fossil fuels will result in less oil refining, and less coke production, and hence a theme within Vianode is circularity and recycling of synthetic graphite.
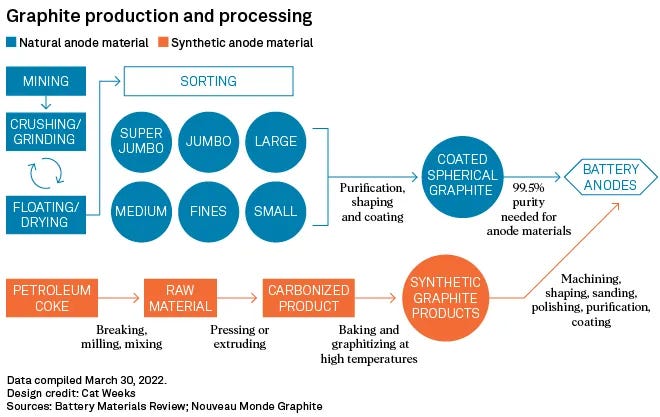
In contrast, natural graphite is mined, and then processed by spheroidising into spheres that perform better than flakes. Generally, the production of natural graphite is a lot less carbon intensive than synthetic graphite. For companies trying to minimise the carbon impact of their cells, this matters a lot.
Synthetic graphite tends to cost slightly less than natural graphite, but with a wider range. You can follow the price point fluctuations in our monthly Battery Component Pricing Reports.
What’s new about Vianode?
In China, synthetic graphite traditionally comes from open-Acheson furnaces, which waste a lot of (often coal fired) energy. In a closed furnace, the graphitisation is insulated and much less energy is lost in the entire process. This is even cleaner if you can use 100% renewable electricity, which Norway has a lot of. Vianode’s breakthrough solution enables synthetic anode graphite offering including a 90% reduction in CO2 footprint on traditional synthentic graphite.
The recent LCA by Minviro assessed their material at 1.9 kg CO₂ emission per kg material, while traditionally produced synthetic graphite has an impact of up to 30 kg CO₂ per kg material. This is paired with European roots making this graphite an appealing ‘derisked’ supply chain.
Work Culture and Daily Experience
I slotted into the office at Kristiansand, was given a standing desk and a hard hat, and was set to work on a project working to screen the performance of different cokes. This involved making a lot of electrodes and cells, and I spent a pleasant amount of time in the lab as well as writing code to analyse my data. I also had lots of time to ask questions and really get my head around graphite a bit more.
The lab was full of characterisation instruments such as XRD, (X-ray powder diffraction which gives the crystal structure of a powder) and TXRF (total reflection X-ray fluorescence analysis for detecting trace impurities), as well as peel strength test (for comparing electrode adhesion) and a coin cell line. Meticulously planned, the lab coats were all dark grey as well as the floors and benchtops (since graphite would never fully come out of a white lab coat).
Going from the individualistic nature of academia into a tight knit and highly specialised team was a huge breath of fresh air. I had my own project, and people to help me get started, but I very quickly felt like I was part of a team. People were happy to answer questions, share lab tasks and help one another out all working towards the same goal. I listened in to the different teams working on different parts of the process and shared my own experience looking after gloveboxes.
I liked how the topics like staff retention and governmental policy engagement were discussed openly and included in the sustainability report. Making sustainable materials also means making a sustainable workforce. The awareness of this was noticeable in the good gender balance.
The Norwegian work culture revolves around an earlier work day than the UK, starting about 8am rather than 9, which I think is due to both the short days in Norway in winter as well as prioritising workers with young children. The company seemed typically Scandi about work hours and schedule. There are no bonus points in Norway for staying late, and the extremely hard working team prioritised getting their work done as well as their health and family life. This strong work ethic was amazing to be a part of, and I felt very motivated and also valued by the very fact I was trusted to get on with it.
From Birmingham to Norway
March to June in Norway gave me the full experience of what felt like three different seasons. In April, I was treated to a sample of Norway’s winter, and May was sunny and bright and around 20-25 degrees with beautiful spring tulips.
I was even lucky enough to be in Norway for Norwegian Constitution day on the 17th May, and enjoyed the city parade full of the local sports clubs and traditional dresses.
I adored the lakes and forests everywhere, and it felt very safe to be a woman out in nature alone. There were lots of clearly labelled trails for hiking, and I spent my weekends visiting local landmarks and tall hills. Kristiansand was even kind enough to open a brand new art museum for my time there, Kunstsilo, and next to it the island of Odderøya seemed to stretch endlessly with German occupation relics strewn everywhere.
The biggest shock about getting back to the UK was the assault on the senses of ICE vehicles everywhere. Kristiansand had a lot of cars, but with 91.5% of new cars sold in Norway being electric, the noise was considerably quieter. The drivers were also very considerate of cyclists, although bikes were mostly segregated off the main carriageway. London and Birmingham were a smelly, roaring shock to the system. It really highlighted the multiple benefits of electrification!
Final thoughts
Graphite is the largest critical mineral component in a battery. Those trying to make the greenest batteries will be focusing on their graphite suppliers as the key place to cut the cell CO2 footprint. With China imposing export curbs on graphite too, graphite production in Europe is one to watch, and I’m particularly excited to see the rise of circular synthetic graphite projects and policies.
My manager at Vianode organised a cake to say goodbye, and I was very sad to leave, especially just one week before the company summer party! If you’re at the early stages of your career and have the chance to do an internship somewhere and try it out, it’s a fantastic chance to figure out what you value in a workplace.
Tusen takk Vianode, and hope to see you again soon!
🌞 Thanks for reading!
📧 For tips, feedback, or inquiries - reach out
📣 For newsletter sponsorships - click here