We recently wrote about different coating and electrode technologies, including artificial SEIs and innovations in aligned graphite. Today, something of interest is the concept of dry electrode manufacturing. But to understand what a ‘dry’ electrode is, we must first understand what today’s electrodes are.
If you enjoy this newsletter, give us a share and subscribe!
🖌️ A background on electrode coating


Aachen University has a visual outlining the main ingredients that go into electrodes. On the anode side, you’ll typically find graphite as the active material and a conductive additive (like carbon black, sometimes a bit of graphene or carbon nanotubes). A solvent (like water) blends and dissolves them, and a binder (like carboxymethyl cellulose and styrene-butadiene rubber) brings everything together. On the cathode side, you’ll find your cathode materials (a blend of lithium and metals) and again a conductive additive. You’ll have a solvent (commonly an organic solvent called NMP) and a binder (such as PVDF).
The role of the solvent in these cases is to combine everything into a slurry and is important to make sure the mixtures are homogenous (aka well mixed across the entire pot). In the cathode, NMP is very effective at dissolving the binder and making slurries, which is why it is commonly used in many battery factories. These solvents are transient, meaning they are used in the coating stage but ultimately dried and removed and not in the final coating product.
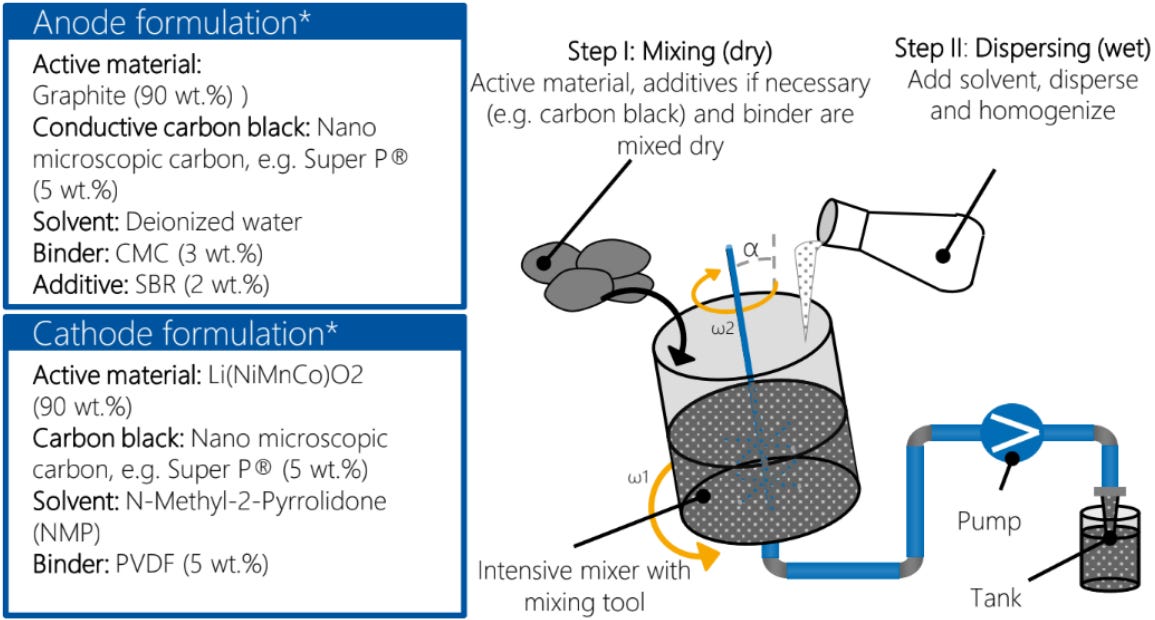
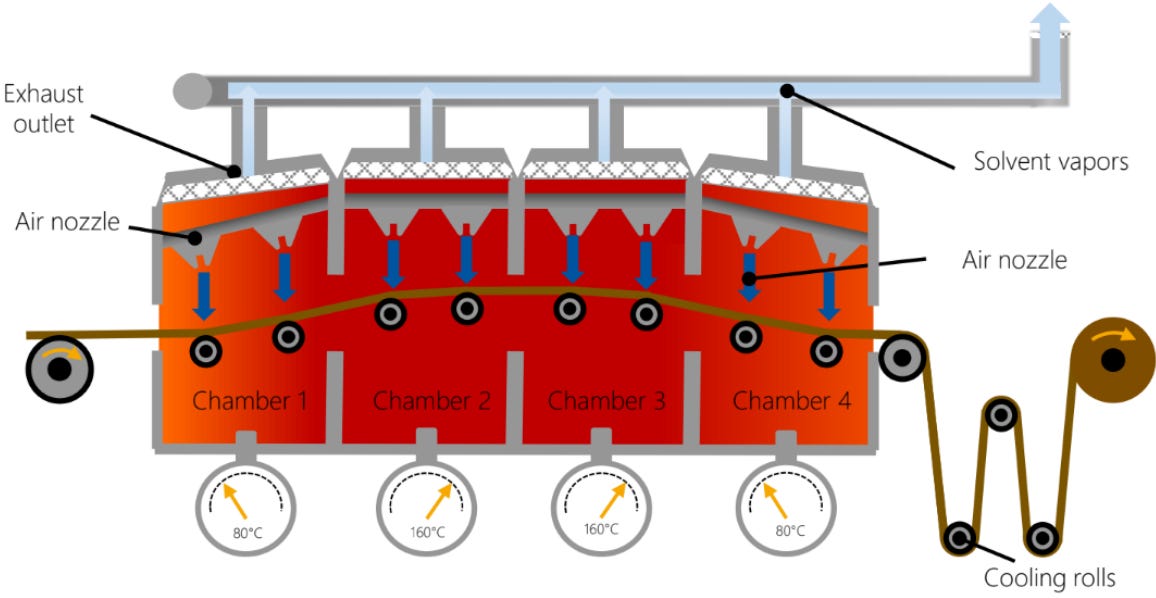
Once these slurries are coated into electrodes, the next step is drying them to make them ready for assembly. Drying processes are generally expensive and energy-intensive. In a BatPac model for a 10kWh battery pack, the drying and NMP recovery process is estimated to be 1.6 and 0.8% of the total battery pack cost respectively, equivalent to $7.8/kWh. Other reports estimate it could be up to 3.2% and 4.6% respectively. What’s staggering is that drying and solvent recovery come out to 46.8% of total energy consumption per cell.
From an environmental standpoint, a 10 kWh battery pack without NMP solvent could save up to 1000 kg CO2 emissions. And to add to the list of cons, NMP is toxic. Note - the numbers above can vary greatly depending on different factories.
⚗️ Dry battery electrodes research
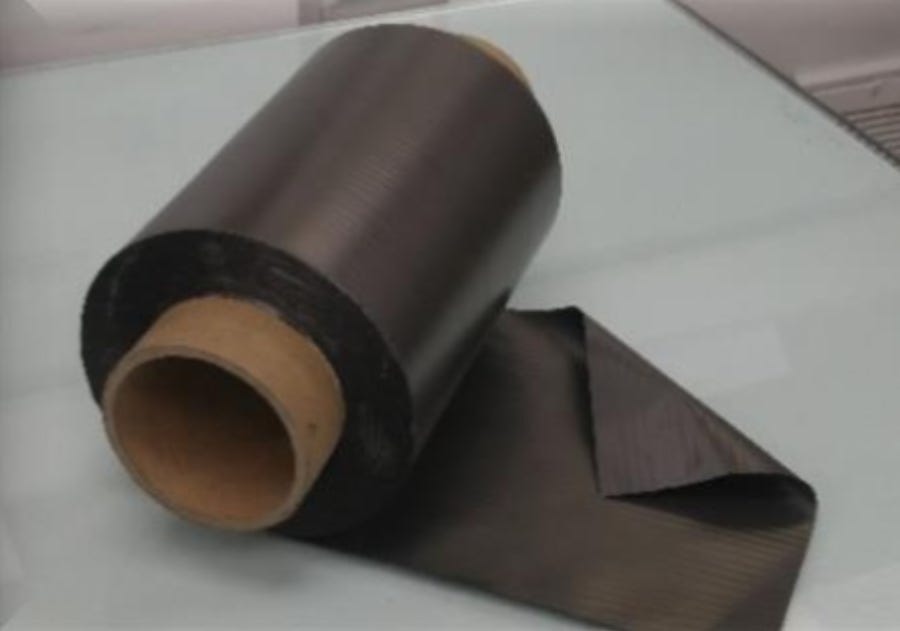
Dry battery electrodes (DBE) have the advantage of evolving from the conventional wet coating methods to make battery electrodes at a lower cost, improved environmental friendliness, and improved electrode performance. On a high level, DBEs could:
Save 19% of manufacturing cost for coating/drying/solvent recovery
Save 47% of energy consumption for coating/drying/solvent recovery
Save 1-2% of raw material costs by avoiding NMP use
Save 19% of capital costs by removing NMP recovery/drying steps
Dry battery electrodes are a new alternative to conventional coatings, demonstrating a ‘‘powder–slurry–film’’ route to the concise ‘‘powder–film’. Borrowing Jill Pestana’s baking analogy, think of this like making your cake batter and layering it. Dry battery electrodes can be manufactured via:
Dry powder mixing. This involves mixing the binder, active materials, and conductive agents (double blade milling, ball milling, etc). It’s important to control the composition and homogeneity of the mixture in this step.
Powder to film formation. There are several processes for this. For example, Maxwell uses flexible binders in the mix (PTFE) which can form connective fibres between electrode materials under shear which may be performed by hot rolling or calendaring e.g at 80 deg C. It’s important to use this process to control and maximize binder fibrillization and film physical properties like thickness and porosity. Dry electrodes cannot be made as thin as conventional slurry-deposited films, but thicker electrodes are more desirable for high energy density. PTFE is not electrochemically stable at the anode and reacts with lithium at low potentials, so dry processing is mainly limited to cathodes. Other binder systems can be used for anodes (link). That isn’t so bad because NMP is the nastiest chemical in the electrode fabrication process and it is only used for cathodes.
Film to current collector lamination executed in a solventless fashion. Once the free-standing film is made, there needs to be a way to layer and adhere to the current collector.
🔬 Who’s researching this space?
Many research groups are working on many aspects of dry battery electrodes, we share a non-exhaustive snippet of the ones we found:
Zhou et al (Jiangsu Universit) demonstrated thick solvent-free electrodes for an LTO/LFP cell.
Shroofy et al (University of Kentucky) showed dry spray coatings for NMC electrodes.
Park et al (German Aerospace Center) worked on dry spraying LTO electrodes.